Design Process
A step through the design process.
Here's an overall of my typical design process. I've taken many products from a sketch through to the production. This has included working with injection moulders, die casters and large scale assembly plants. I'm happy to pick up projects at any stage of the process and take them to the next stage or through to completion.
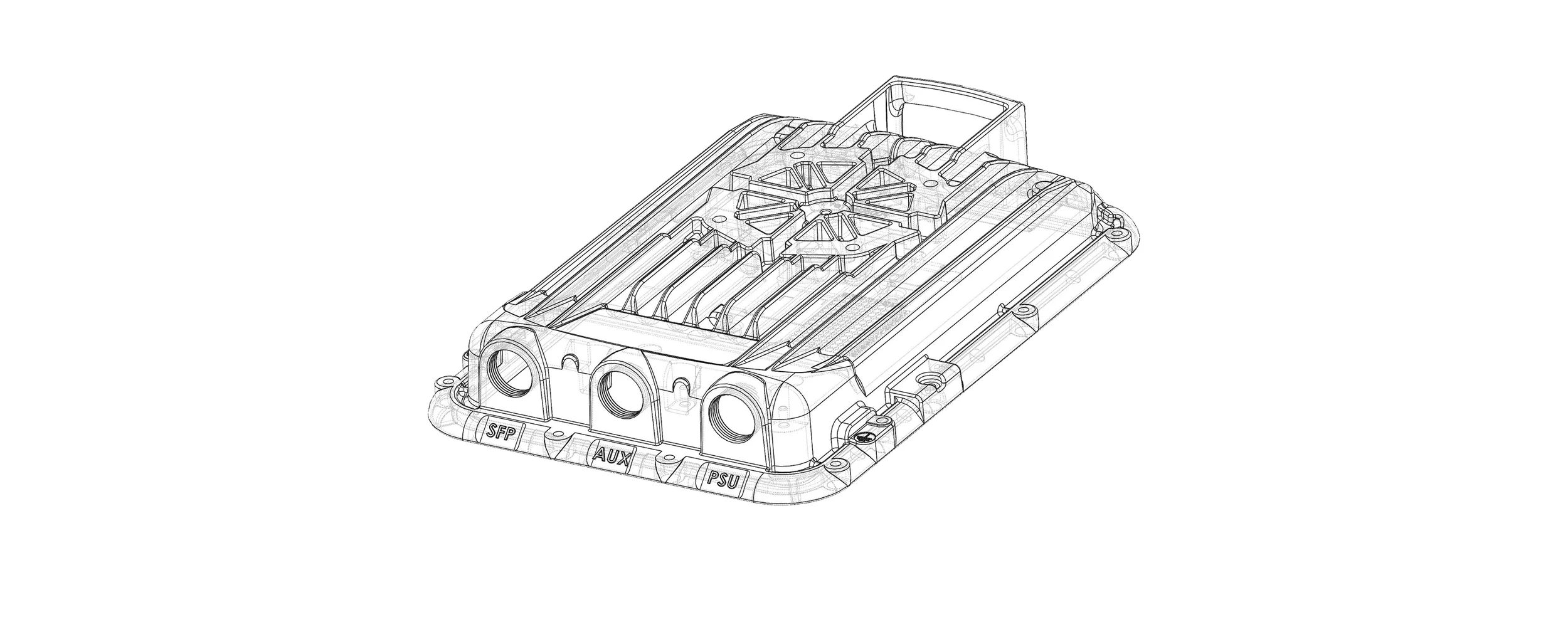
CONCept stage
Research
Understanding the market and requirements for the product is key to a successful design. Research often opens up other ideas and ways of viewing the same problem from a different angle which often leads to innovation. Researching how competitors have solved similar problems saves design time and helps to ensure the design has a competitive edge by learning from others.
Evaluating market treads
Critical analysis of competitors’ products
Defining key market / product requirements
Compiling a product design specification
Ergonomic and anthropometric data analysis
Concept + Creative Thinking
Using the research and a product design specification as a guide concepts for the product can be created. This is often broken down into different areas so that concepts can be created for specific areas. For example the overall aesthetics of the product, specific technical challenges and customer interfacing areas.
Concept generation
Sketches
3D block models finished and painted to get an idea of form and styling
Concepts looking at a specific detail whether its technical or aesthetic related
3D CAD rendered models and drawings for presentations
Concept evaluation / selection methods
Financial evaluation of concepts

design stage
Initial Design + Prototyping
This is where a digital 3D model of the chosen concept is created. Often prototypes of specific areas or functions are created using rapid prototype techniques. This can be using a DFM machine or milling from solid if specific material characteristics are required. These physical models help to gain a great understanding of what is possible and a direction for the design.
3D digital modelling of initial design
Functional prototypes of specific areas of design to help evaluate concept suitability
3D physical models to get an idea of size and form
Working with the prototypes and customers to great define the product requirements
Working with manufacturers to ensure cost effective designs
Detail design Engineering
Devils in the detail! This is where the initial design is fully defined in a digital 3D model. Every aspect of the design is considered and constrained. This is often takes the most amount of time but if done well will save significant amount of time in the future and the manufacturing stage.
Mechanical design
Creating 3D digital models for evaluation
Creating 2D technical component and assembly drawings that can be used for quotation with manufacturer
Stress analysis with 3d digital models
Hand calculations
Defining materials and specific manufacturing techniques
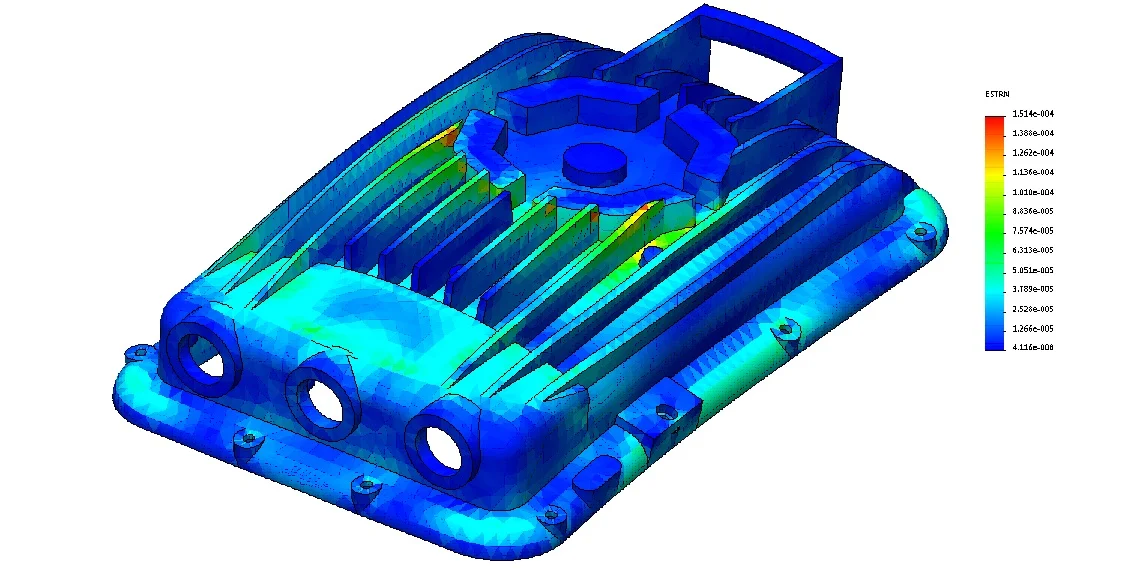
testing
Design Verification
Close to production intent prototypes are tested to verify that the design meets the requirements set out at the start of the project. The testing looks at the performance of the product, life and fatigue of the product through to transportation testing. Tests are generally from ISO standards, MIL standards or tests defined with the customer.
Produce production intent prototypes through using rapid manufacture techniques. Soft tooling and machined parts
Design and setup of test fixtures to aid the product testing
Working with test houses to product tests to required specifications
Manufacture
Over the years, I've spent a large amount of time visiting factories to really understand high volume manufacturing techniques so I am able to design products for ease of manufacture and assembly.
Manufacturing Support
By this point manufacturers will have seen and fed back into the design to ensure it is suitable for manufacture. This stage is where the tools are designed by the manufacturer there is a close liaison between the designers and the manufacturer to ensure critical parameters of the design make it through to the production parts.
Select manufacturers low to high volume – UK or overseas based
Working closely with the manufacturers to help the design through the initial manufacturing stage
Validate first off tool parts and sign off parts for production
Visiting factories to validate manufacturing methods
Ongoing Support
Designs can always be improved with time. Feedback from the market or advances in technology can push designs forward. This is the section where improvements are evaluated and fed back into the design.
Evaluation of customer feedback
Possible changes evaluated both from a financial and design perspective
Generate concepts and drawing to show customers or manufacturers the potential improvements